Analysis and Estimate for an Economical Residential Structure Using Alternative Building Techniques
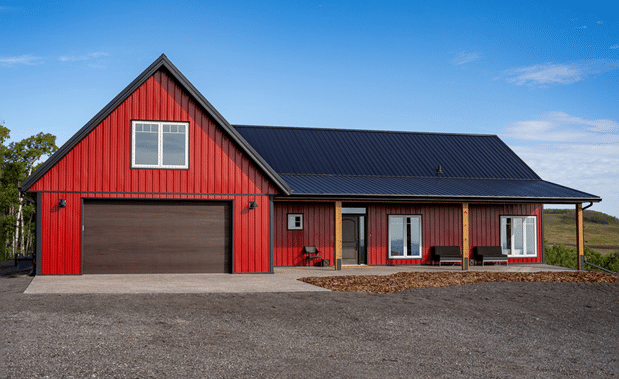
Mark David Alejandro
Andrei Charles Atendido
Laura Danielle Hearn
Mikayla Gayle Manky
ANALYSIS AND ESTIMATE FOR AN ECONOMICAL RESIDENTIAL STRUCTURE USING ALTERNATIVE BUILDING TECHNIQUES
A Capstone Project Presented to the
Faculty of Civil Engineering Technology
School of Construction
Southern Alberta Institute of Technology
This Capstone project is written for Integrity.
Written by
Civil Engineering Technology – Construction Management students:
Mark David Alejandro
Andrei Charles Atendido
Laura Danielle Hearn
Mikayla Gayle Manky
Ben Ellard
Capstone Adviser
Karen Riley
PROJ 386 Instructor
April 12, 2024
EXECUTIVE SUMMARY
Building techniques and methods in residential construction have always been the same through the years, these techniques served as a staple in the construction industry. This is the basis to observe that there are only limited ways in which we can construct a residential building. However, with the help of some innovative minds from people in the industry, new building methods and techniques have been slowly becoming recognized especially since there are new technologies and materials that can be substitutes to traditional building methods. The main objective of this study is to investigate and analyze alternative building techniques done by Integrity Builders Ltd, as well as present a recommendation for a more economical building method. The focus is to analyze and highlight Integrity’s building techniques such as their Perma-columns, frost shields, and wall systems. Implementation of these techniques are also being analyzed as the efficiency and effectiveness of these are quantified through thermal scans, R-value calculations, and cost estimations.
Integrity Builders use a post-frame technique as an alternative to a traditional stick-built method. This consists of a pile foundation using pre-cast Perma-columns and a slab on grade. The slab must be protected from frost heave, so Integrity created a frost shield that protects the slab and helps insulate the building. From the Perma-columns, the structure is composed of built-up columns with strapping on the exterior side, spaced at two feet on center. These few alterations from traditional building techniques have the potential to greatly improve the way that we build and that is what will be explored in this study. The aim of changed construction practices is to either lower the initial cost or raise the energy performance of the building, which would ultimately lower the long-term costs. Innovation and a willingness to do things differently is how the construction industry can improve and this study will give both builders and homeowners some insight into the opportunities to build better.
To validate one of the objectives of this study, the team conducted thermal scans on one of Integrity Builders’ projects. It was considered that the techniques that were implemented on the project use the post-frame method to have a better analysis of the behavior of heat that can be present in this method. The thermal scan was conducted by taking thermal images with different types of drones and these images are analyzed by using FLIR Tools – a software that can analyze and present thermal imaging data. Results from these scans exceeded the team’s expectations since there was barely any heat loss that was present in the scans. However, it can still be improved by making sure insulation is properly installed and even installation of exterior insulation can highly improve the efficiency of this technique. To have a deeper understanding of this concept, R-values were also calculated and compared with the traditional stick-built method. The R-values between the two techniques had a significant difference with post-frame structures having higher R-values compared to the other technique. With the findings in this research, it can be determined that even with just the designed wall assembly with proper insulation, post-frame structures are superior when it comes to thermal performance.
With post-frame structures having a better thermal performance than the traditional stick-built method, analysis of the cost of construction is vital to properly quantify the economic impact and cost differences between these techniques. The costs for this research are gathered from Mattamy Homes for their prices on traditional stick-built construction and Integrity Builders for their prices on post-frame construction. These estimated costs are determined that both techniques comprise similar uses and components of a home to make a more accurate depiction of their economic value per square foot. Furthermore, with the costs that both techniques analyzed, it can be concluded that post-frame construction is cheaper than the traditional stick-built since fewer materials and labour are used with the post-frame. Furthermore, the cost savings from this method can be used for additional protection and improvements for the structure, thus making it more stable and efficient than the traditional technique.
After all the research and analysis of the distinct differences between the traditional stick-built method and the post-frame method, the team has identified a few recommendations to further develop this study or make their study out of this. Firstly, Integrity introduces a whole different concept of construction, therefore, having various building techniques to be researched. Thus, being able to analyze the costs and efficiencies of other techniques aside from the ones discussed here, will be beneficial in transforming the way of building. Next, being able to incorporate other disciplines such as mechanical, architectural, and electrical will bring this study to a whole different level. As this study only focuses on structural, different improvements and estimates can be made when different disciplines are being incorporated with one another. For example, the installation of radiant heating and tankless hot water tanks can increase the overall efficiency of the house and could help homeowners save money on water and heating bills. The implementation of geotechnical studies and high-performance studies in alternative building techniques done by Integrity will identify if these foundation techniques are suitable for the type of soil here in Alberta. High-performance standards are then set by qualified institutions that will certify these techniques or if not be able to make necessary changes and alterations to make these techniques high-performance. This study is the initial step in analyzing new building methods done by Integrity Builders and the team hopes that this study will continue and serve as a guide for future researchers to find the most efficient and economical building method there is.
TABLE OF CONTENTS
EXECUTIVE SUMMARY ii
TABLE OF CONTENTS iv
LIST OF ILLUSTRATIONS v
LIST OF TABLES v
1.0 INTRODUCTION 1
1.1 Purpose 1
1.2 Background 1
1.3 Scope 1
1.4 Methods 2
1.5 Preview 2
2.0 INTEGRITY BUILDERS DESIGN 3
3.0 THERMAL SCANS 7
4.0 COST ESTIMATES 10
4.1 Stick-Built 10
4.2 Post-Frame 11
5.0 ANALYSIS 13
5.1 Building Technique Comparison 13
5.2 Cost Comparison 14
5.3 Performance Comparison 15
6.0 CONCLUSION 17
7.0 RECOMMENDATIONS 18
8.0 ACKNOWLEDGEMENT 19
REFERENCES 20
GLOSSARY 21
APPENDIX A: Ridged Insulation Assembly A
APPENDIX B: Example of Thermal Analysis Using FLIR Tools B
APPENDIX C: R-Value Calculations C
APPENDIX D: Cost Estimate for a Traditional Stick-Built House D
APPENDIX E: Cost Estimate for Integrity’s Post-Frame Construction E
APPENDIX F: Continuation of Cost Estimate for Integrity’s Post-Frame Construction F
APPENDIX G: Gantt Chart G
LIST OF ILLUSTRATIONS
Figure 1. Perma Column 3
Figure 2. Column Strapping 4
Figure 3. Frost Shield 5
Figure 4. Ice lenses and Capillary Rise of Water 6
Figure 5. Heat Flow Diagram 6
Figure 6. Zenmuse Drone with 13mm and 19mm Cameras 7
Figure 7. Autel EVO Drone 7
Figure 8. Stick Built Residential Building 10
Figure 9. Integrity Builders Techniques Implemented into a Residential Building 12
Figure 10. Cost Comparison Between Stick-Built and Post-Frame Construction 15
Figure 11. R-Value Graph Comparison 16
LIST OF TABLES
Table 1. Temperatures of Building Components 8
Table 2. R-Values of Building Techniques with Different Spacings 9
Table 3. Cost Break Down of Stick-Built Homes 11
Table 4. Cost Breakdown of Post-Frame Homes 12
1.0 INTRODUCTION
This project is the analysis and estimate for an economical residential structure using alternative building techniques from Integrity Builders Ltd. The team will specify further throughout this document that the purpose of this project is to give insight into alternative building practices that can be adopted by builders and homeowners for future residential designs.
1.1 Purpose
This study aims to investigate and analyze the thermal performance and cost efficiency of residential building techniques done by Integrity Builders Ltd and compare them to traditionally built homes. Introducing this method and using the research, plans, and estimates produced in this study will be beneficial to the contractors as well as homeowners who would want their homes to be more efficient and economical.
1.2 Background
North American residential homes have been built the same way for many years. This leads to curiosity about why we build this way, and whether it can be done better. Additionally, considering the national housing crisis, the second question arose, was there a way to optimize the performance of residential homes and achieve this at a more economical cost for users? During the Civil Engineering Technology program, the team has built a basic understanding of building materials, design and drawing technology, and construction processes. With this knowledge, further investigation occurred on how residential construction can be optimized while maintaining cost efficiency. During this research, the team found a relatively new practice called “post-frame” that completely alters the main frame of the building. Traditional homes are built using the “stick built” method. This method uses a concrete foundation, typically including a full basement preceding walls are built piece by piece from dimensional lumber such as 2x4s or 2x6s. The post-frame structures were first used in barn or shop applications but have recently been adopted in residential construction because of their cost-effectiveness. Post-frame structures differ essentially by the frame being columns extending from the foundation’s base to the roof. This method cuts material and labour costs, leaving more room in the budget to encompass more building sciences to produce a higher-performance home, and in turn, lowering maintenance and energy costs for the owner.
1.3 Scope
This investigation will explore the building techniques and technology that Integrity uses and how to implement these in our future projects. The team will analyze the structural components of a residential home within Calgary using practices from Integrity Builders and estimate its costs. Included in the project will be a mock design, cost estimate, thermal scans, and research around the technology that Integrity uses. Furthermore, comparative analysis will be done with traditional building techniques. It will not, however, include any architectural, mechanical, or electrical designs or speak about how these techniques can be adapted for other locations outside of the Calgary area. These aspects that the team will be addressing are important for Calgary builders and homeowners to explore their options for upcoming projects and give insight into alternative options for structural design.
1.3 Methods
Quantitative data study, comparative studies, and interviews are the research methods that will be used in this study. Each method is used in a way that will provide the team with the data needed to determine the sustainability and efficiency of the proposed residential building. For interviews, this was done by scheduling meetings with Carleen Grant and other key people from Integrity Builders Ltd. Also, meetings and interviews with the team’ SAIT professors such as Ben Ellard, the team’s capstone advisor for clarification of Estimating methods, and Matthew Eidt for Building Science concerns. Interviews with Matt Harding from Mattamy Homes were also done to have a more accurate quote on the cost of traditionally stick-built homes. For the quantitative data study, the team will be conducting site visits, interpreting shop drawings and plans provided by Integrity Builders Ltd., and performing scans and tests on Integrity’s residential buildings. These tasks will be done by construction standards that are set by Surveying, Construction Practices, and Building Science. Finally, comparative studies will also be done by identifying differences between Integrity’s building techniques and traditional building methods. These differences will be identified through thermal analysis and cost estimates. The data gathered will then be used in creating a feasible mock design using Revit that properly caters to this project’s purpose. Then, the team will gather a detailed estimate of different structural components from various sources to determine the economic value of the residential structure. Finally, the results from the building design and estimates will be analyzed and compared to determine the applicability, efficiency, and economic impact of the recommended building technique.
1.4 Preview
This research project will follow the whole process the team took to provide the reader with the analysis of Integrity’s building technique that is applicable and economical to residential construction. The report will detail the following:
- Detailed overview of Integrity Builder’s design.
- Thermal scans provide information about the energy transfer of Integrity’s building methods as well as R-values.
- Cost estimate of a design implementing Integrity’s building techniques in comparison to a traditionally built home.
- Analysis and summary of all findings and options.
- Conclusion detailing all variables detailed in the report.
- Recommendations on building materials, methods, standards, and performance.
2.0 INTEGRITY BUILDERS DESIGN
Integrity Builders use a combination of their technology and alternative building practices in their designs to create structures that serve the same purpose as a traditional stick-built home but can be built more economically, more energy-responsible, and with faster construction times.
The main difference is that Integrity’s design uses a column system instead of studs and a basement foundation to comply with their alternative foundation. These columns function as the main frame of the wall as well as the foundation. They use Perma-columns to create a pile foundation, which extends 5-7 feet below ground level and protrudes directly to the top of the wall frame. This comprehensive design allows for lower construction times since the wall frame and foundation are installed at the same time. It also lowers the overall cost since no excavation, cast-in-place concrete, and backfill or surplus are needed. Perma-columns combine the use of precast concrete, steel, and wood to produce a durable and cost-effective building product. These are installed using a drilling rig. Once the site has been surveyed and locations for the columns have been determined, the drilling rig comes on-site and effectively drills all the holes. Once the driller has finished, they may leave the site, allowing workers to begin to erect the columns and backfill the holes with coarse granular gravel that ultimately locks in the column and continues to gain stiffness as settlement occurs. These Perma-columns are available from the manufacturer in Indiana; however, Integrity Builders owns the rights in Western Canada, and therefore independent builders can purchase them through integrity, rather than importing them from the United States [J. Myer, private communication, November 2023]. Perma-columns as seen below are a high-quality product, and as stated on the manufacturer’s website “this innovative approach protects the structural integrity of the foundation, protects your customers building investment and your reputation as a quality builder” [1].
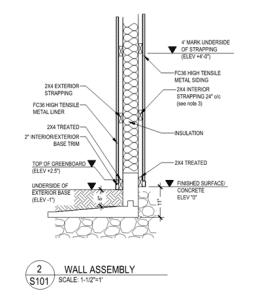
Figure 3 above shows how the frost shield is used in a wall assembly. Using the frost shield prevents damage to the slab by stopping the frost from being able to get below the structure as frost can only travel at a forty-five-degree angle and is unable to get around the Styrofoam wedge [J. Myer, private communications, November 2023].
Additionally, as this study is conducted in Canada wherein the country experiences below-freezing temperatures (0°C / 32°F). Specifically in Calgary, the city experiences these temperatures each year generally from November to March [10]. This contributes to the presence of potential frost heaving in the structures. Frost heaving is the freezing of moisture in the soils effectively creating ice lenses that cause the foundation to move upwards due to the swelling along with the capillary action from the water in the groundwater table increasing the mass of the ice lenses which will affect the structural integrity of the building. As the temperature rises, the ice lenses melt, and the soil shifts back downwards to its original position which causes an upward-downward movement in the freeze-thaw cycles [9] (Refer to Figure 4 for illustration). Due to this mechanism, builders are required to build below the frost line to prevent this from happening.
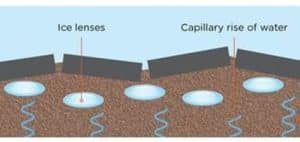
The main purpose of the frost shield built into the wall assembly is for the protection of the superstructure from frost heaving. To deepen the understanding of this concept, the team borrowed concepts from the Revised Builder’s Guide to Frost Protected Shallow Foundations [11]. It allows Integrity to build shallow Perma-columns instead of the traditional deep foundation walls as the frost shield, along with the radiant heat from the building, raises the frost line. The heat loss from the building through the floor assembly warms the soils underneath the structure along with the geothermal and radiant heat while the frost shield traps the heat underneath this structure and redirects the heat flow around it. This heat is what effectively raises the frost line and allows for shallow foundations (Refer to Figure 5 for diagram).
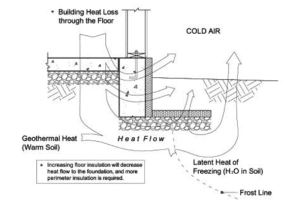
3.0 THERMAL SCANS
According to the Department of Energy, thermal scans measure surface temperatures using cameras. Thermal imaging cameras are commonly used to locate and identify building failures as they let the user identify and analyze everything it captures. Thermal images are the result of thermal scans, these are pictures that display a visual representation of heat presence ranging from cooler to warmer regions. These thermal images serve as an identifier of the effectiveness of the building’s insulation, energy efficiency, and performance. Also, thermal scans can detect air, energy, and thermal leakages through doors, roofs, walls, or any component of the house [5]. Thermal scans and images are versatile tools for high-performance construction as they not only determine a structure’s efficiency but also identify areas that require improvement.
In this study, the team went to one of the residential projects done by Integrity Builders in Okotoks, Alberta to conduct thermal scanning. With the help of Rick Duchsher, SAIT’s resident drone pilot, the team was able to capture thermal scans of roofs as well as walls of the residential property. The purpose of the scans is to analyze the thermal properties of the building and eventually suggest improvements that can be made depending on the results of the scans. Two different types of drones were used in conducting the scans to identify if there were visual differences between the two. As seen in Figure 6, the team made use of the Zenmuse Drone with 13mm and 19mm cameras attached to it. This drone provides visual representation as well as accurate values of temperatures in captured surfaces. The team also used the Autel EVO drone (figure 7), however, this drone provides thermal images only.
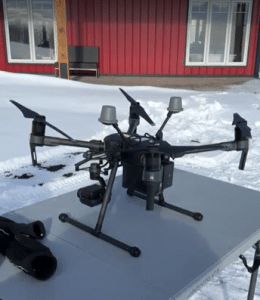
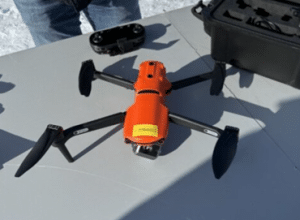
Source: Primary
After conducting the thermal scans, the team extracted data from thermal images using FLIR Tools. FLIR Tools is a software that reads and analyzes thermal images by changing them to appropriate color palettes, adjusting thermal parameters such as emissivity, and displaying necessary information for thermal analysis (refer to Appendix B for example). Below is a table of temperature readings of different components of the residential building from the 13mm and 19mm cameras.
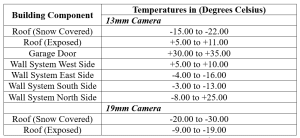
From the data presented in Table 1, it shows the various temperature scales of different components and sides of the residential area. It is also important to take note that the temperature condition on the day of the thermal scan is -8.00 degrees Celsius and the weather is sunny. Ambient temperature and site conditions are necessary since these factors can influence the gathered temperature data. Furthermore, data shows that the 13 mm camera was used to cover the scans surrounding the residential building and the 19 mm camera was used to gather detailed temperature range of the roof. The causes of temperature differences of every component that was gathered from the thermal scans are the reflective sunlight, ambient temperature, building material of the component, and internal insulation of the building.
As seen in Appendix B, thermal images in the facade area of the residential structure, although it seems like heat leaving, based on careful analysis, is heat that is gained due to the sunny weather during the time of thermal scanning. The wall assembly that was used in this project consists of a thermal membrane, rigid insulation installed in wall panels, and a hi-tensile metal panel. These components contribute greatly to preventing heat loss and thermal bridging. Regarding the thermal images, it can be concluded that through visual inspection and observation, the differences between temperatures are caused by the metal panel’s properties where it can absorb external temperatures. Also, with the help of the insulation and thermal membranes installed, it prevents absorbed heat from further going into the structure. Moreover, for the roof of the residential structure, there is a slight temperature difference in that area. This is due to improper installation of the spray foam insulation. However, even though there is a slight temperature difference in that area, there is minimal heat loss since the material used for the roof, which is like the wall assembly, prevents heat from going out while absorbing heat. Overall, this residential house was constructed to minimize heat loss and therefore conserve power and energy.
Analysis of the thermal scan data of a typical traditional residential building here in Canada was done, this data was gathered from Patrick Lejtenyi’s research from Concordia University. Based on their findings, older residential buildings tend to have older insulation whereas some are poorly insulated. This usually results in more heat loss throughout the structure, thus resulting in more than a quarter of low-income tenants’ incomes [7]. Moreover, to have a more accurate comparison with the post-frame structure by Integrity, stick-built homes generally experience a difference in heat loss by as much as 30% [7]. This is identified by using the product of the building’s surface areas, temperature differences of design and outdoor temperatures, and overall R-value. Having a 30% heat loss can have a big impact on the overall performance and efficiency of a building and with the use of Integrity’s techniques, homeowners can prevent having that amount of heat loss in their homes. However, identifying that heat gain and loss are not the only factors in determining a structure’s performance and efficiency, but also being able to compute and identify the R-value of a residential component as these values go hand in hand in determining a structure’s heat gain/loss.
R-values, as defined by Al-Homoud, stand for the measure of the level of thermal resistance of a component, material, or assembly [8]. This is primarily about the conductivity of heat wherein the R-value is directly proportional to its thermal conductivity, meaning the higher a component’s R-value, the better its insulating performance. This suggests that the R-values of components determine how efficient and economical a structure is. Thus, the team has done calculations of R-values for both Integrity’s building techniques and a traditional stick-built structure, this is to have an accurate comparison of the thermal resistances of each building technique.
The R-values computed for Integrity’s post-frame house and a traditional stick-frame house were based on a simplified wall assembly portion with no windows or doors. Each considers only wood framing, and R20 fiberglass batt insulation in the wall cavity and or airspace. First, the percentage of wall framing was calculated for the two different wall assemblies. The way in which the percentage of framing was calculated was by taking a portion of the wall, either using the area between 2 columns or 2 studs. When the total area was calculated, the area for 2 columns or 2 studs were calculated, this number was divided by the total area resulting in the percent framing. Second, each material’s thermal resistance was found using part 9 of the NBC 2020. Finally, each calculation used the percent of framing along and the percent of wall cavity along with the material thermal resistance values obtained from the NBC and inserted into the RSI parallel equation to produce a value for one homogenous layer. Furthermore, the detailed calculation of these R-values is found in Appendix C.
Table 2. R-Values of Building Techniques with Different Spacings
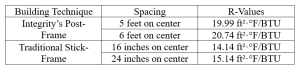
It can be concluded from the calculations and values in Table 2 that a post-frame structure is undoubtedly more energy efficient due to the more thermal resistive wall assembly. Therefore, it is evident that post-frame structures can be around 31% – 35% more efficient than a traditional stick-frame house.
5.0 ANALYSIS
In this study, the team compared a post-fame building by Integrity to a mass residential builder local to Calgary. Each of these projects has been chosen based on criteria to accurately represent a cost comparison. This criteria’s main consideration was square footage. The goal was to compare two 1500-2000 square foot residential buildings’ costs to each other. The reason why square footage was the main consideration is strictly for owners living space. This study ultimately is to show a homeowner the economic advantages of choosing a post-frame building over a stick-frame building. Since the main consideration was square footage there will be some other differences in design between these two buildings. The main differences include the following: the number of floors, roof area, and basement usage. The basement in the stick frame building is not considered part of the square footage since it serves the primary purpose of a foundation for the living structure above. This is a common industry standard.
4.1 Stick-Built
Traditionally homes in Calgary are built with a full basement consisting of concrete foundation walls supported by a strip footing and a slab on grade sitting within the walls. From there a subfloor is constructed on top of the walls, it is built out of rim board, engineered floor joists, and topped with either plywood or OSB sheathing. The walls are built on the ground flat and are stood up in place, made of a bottom plate on which the studs sit, and have two plates on top. The subfloor and wall system can be repeated for additional floors until finally engineered trusses are installed for the roof. This has proven to be a consistent and effective method and as such it has been implemented for a very long time. However, the excavation of such a large area, large amounts of lumber used, and such long on-site construction times raise the price substantially.
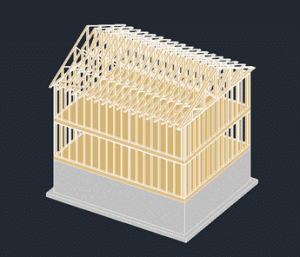
The costs associated with this method can be seen in the table below:
Table 3. Cost Break Down of Stick-Built Homes
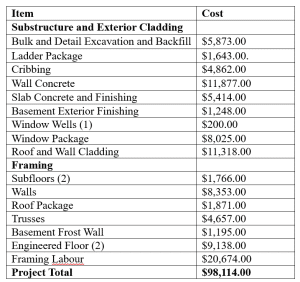
Table 3 gives a breakdown of costs from a mass residential builder in Calgary. These costs were obtained through an interview with the head project manager who provided cost categories for a previous house they completed within the last year. This list makes up just the structural components and the exterior shell of the home to get an accurate comparison of the home that integrity delivers. This includes the foundation, unfinished walls, roof components, exterior shell, labour, and any costs associated with these items. This 2-storey, 1597 square foot stick-built house comes in with a total of $98,114.00, providing a price per square foot of $61.44.
4.2 Post-Frame
Integrity Builders use an alternative method that has many cost benefits. Instead of having a full basement, they utilize the technology of frost shields to make it viable to use a pile foundation. This means that a lengthy and expensive excavation can be replaced with auguring pile holes in which precast Perma Columns can be placed. The difference in the foundation reduces excavation time to one day, removes the cost of casting the frost walls and strip footing on site, and substantially lowers the labour costs involved. From there wooden columns are placed within the metal brackets on the top of the Perma Column piles which become the primary structural components of the wall system. For lateral stability strapping made of two-by-fours is installed on the outside of the columns spaced at two feet on center. Using this wall system reduces the amount of lumber in the wall assembly which both lowers the cost and the thermal bridging, making the wall cheaper and more energy-responsible. To finalize construction, engineered trusses are placed at the same spacing as the columns, which again results in a much lower cost as they can be spaced further apart. Over all the techniques used by Integrity Builders will lower on-site construction times and remove the necessity of mass excavation and large amounts of lumber.
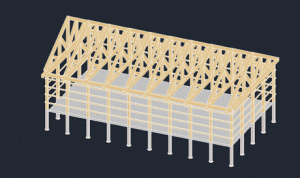
Source: Primary
Costs for this alternative building method can be seen in the table below:
Table 4. Cost Breakdown of Post-Frame Homes
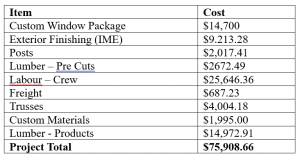
Table 4 provides a cost breakdown from Integrity Builders. This information was obtained through several meetings with the sales representative, head estimator, and CEO of Integrity Builders. This is the cost breakdown of everything Integrity provides to bring their design to the lock-up stage if the project were to take place currently. This includes only the structural components as well as the exterior shell. The list covers the Perma-Column foundation, wall assembly, roof components, exterior shell, labour, and any other associated costs. This single-story design is called by Integrity “The Bunkhouse” which provides 1905 square feet of living space. The total cost of this building comes to $75,908.66, providing a price per square foot of $39.85.
4.0 COST ESTIMATES
One of the objectives of this study is to analyze the differences between post-frame construction by Integrity Builders and a traditional stick-built method. This comparative study was completed using thorough research and data gathering from various sources. From data that was gathered throughout this study, the team identified three new building techniques for post-frame construction that were taken from Integrity’s construction philosophies – application of frost shields, use of Perma-columns, and external strapping installation. These techniques were then used for a design through a Revit model to properly illustrate and help the readers distinctively visualize the techniques. Also, cost estimates, thermal scans, and R-value calculations were gathered to properly compare and quantify the economic impact and performance of the two techniques.
5.1 Building Technique Comparison
Before conducting economic and performance analysis, the team first must identify the differences in building techniques between a post-frame construction and a traditional stick-built construction. These techniques were identified and chosen for the main purpose of cost reduction while achieving a more efficient structure. Furthermore, comparing these techniques will help introduce a new way of building our residential facilities and identify its applicability to our current or traditional way of construction.
Firstly, the application of Perma-columns on post-frame construction serves as both the main framing and foundation system of the structure and is installed by drilling holes into pre-determined locations, then, posts made of concrete, steel, and wood are placed and packed. The main difference of this system to the traditional installation of strip footing is the way of carrying its load: post-frames are like stilts and strip footings are like rafts that support the total load of the structure. Unlike strip footings, where excavation is needed for its installation, these columns are placed into drilled holes in the soil thus speeding up construction times and reducing material and labour costs. However, since these columns do not provide good protection from frosts unlike strip footings where frost walls can be installed, Integrity’s technology came up with frost shields – the second building technique the team focused on.
Installation of frost shields complements Integrity’s building techniques since this protects the slab on grade and pile foundations from frost heaving and cold temperatures from the outside environment. Furthermore, this also prevents concrete in slabs as well as in Perma-columns from experiencing freeze-thaw that can damage the durability and quality of concrete. Even though frost-shields are still patent-pending, several projects have already proven their capabilities like the residential project discussed in the thermal scans. It depicted an excellent example of preventing heat loss and frost heaves from entering and leaving the structure as seen in the temperature and thermal data that were collected in the thermal scans. On the other hand, traditional stick-built structures make use of foundation walls and the installation of insulation in between frost wall studs. In some cases, insulation is also installed underneath the slab as this prevents frost from entering the concrete even though basement depths are well beyond the frost line. These differences between techniques almost serve the same purpose as both techniques have
the main objective of preventing external temperatures from affecting the durability of the materials underneath the soil.
Lastly, Integrity utilizes wood strapping in its building techniques. Unlike traditional stick-built techniques where strapping is just a support whenever exterior insulation is applied in the building, wood strapping is essential in this specific technique. The strapping used in post-frame construction serves as a fastener for cladding making sure it is acceptable to specific requirements for cladding support and as a lateral support for the Perma-columns. Having this component as a major and necessary structural element provides not only additional support but also is essential to meet requirements for structural bracing.
These differences between techniques prove that new technologies and methodologies can be developed that perfectly integrate with how Integrity builds. It can serve the same purpose as the traditional method or make an optional component translate into a major role in the structural durability of a residential structure. Having achieved and analyzed these techniques, it is important to take note that the cost and efficiency of the alternative practices are, if not equal, surpassing the overall quality of construction.
5.2 Cost Comparison
Construction cost is always one of the determining factors whether a client or a contractor accepts or rejects a specific project, whether it is for a residential, industrial, or commercial project. Integrating cost analysis to compare two different building techniques allows the team to properly quantify the economic impact and cost differences between these techniques. Moreover, the team set a few parameters to make this comparative analysis more accurate: the total floor area for both construction projects ranges from 1500 – 2000 ft2 and construction costs only include the foundation, wall assembly, subfloor with roof, overall substructure, exterior shell, labour and other associated costs to these components. It is important to consider that no additional construction costs are calculated to have a closer comparison using these two techniques. After setting these parameters, the team reached out to Mattamy Homes and Integrity Builders to ask for an accurate cost estimate on a typical stick frame construction and post-frame construction respectively. Detailed and accurate cost estimates can be found in Appendix D and E.
This comparison has a few differences to note in the methods of data collection and analysis. First, the stick-built house’s estimated costs associated with the basement foundation include all labour, the only cost that is separated from the materials is the framing labour. Therefore, it would not be accurate to directly compare this labour cost to the one that Integrity provided, as their cost is all labour included in the construction. Additionally, due to the nature of the difference in construction methods and sequence in the two buildings, the foundation costs should not be directly compared. It is recommended that the reader acknowledges the cost breakdown for each building technique but focuses on the final cost as well as the price per square foot to conclude.
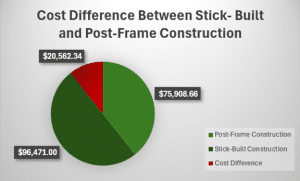
Figure 10 illustrates the cost difference between the two techniques. It can be identified from the graph that building using the post-frame technique saves clients approximately $20,562.34 on the cost of construction. Post-frame structures being cheaper than the other proves that this building technique is more economical and cost-efficient. It should also be noted that these costs only include certain building components and not the total cost of the structure. Thus, it is recommended to have more detailed cost estimates between techniques from foundation to finish to determine a more accurate cost comparison. However, these costs spent for post-frame construction are seen to be more viable and economical than traditional methods.
5.3 Performance Comparison
As defined by Joe Di Noto in a blog post [4], “High-performance buildings are structures which are designed and operated in ways that optimize energy efficiency, minimize environmental impact, and promote a healthy indoor environment for occupants.” As also highlighted in this post the 3 critical factors when it comes to defining a High-performance building are its energy efficiency, environmental impact, and healthy indoor environment. Ensuring that a structure is up to high-performance standards helps in several ways to the occupants and/or its owners. Some of these benefits include but are not limited to [4]: lower operating costs, increased property value, improved productivity, and higher tenant satisfaction.
High-performance standards in buildings are not just parameters or criteria to achieve but a set of practices that attain the title. Plenty of organizations advocate for the creation of structures that follow these standards using sustainable materials, using building techniques that reduce the creation of waste and pollution. Organizations such as the Leadership in Energy and
Environmental Design (LEED), Living Building Challenge, and Zero Net Energy Building are found across the world that promote this practice and certify buildings that uphold green standards. There are benefits and drawbacks to this standard with the latter having lower annual costs due to higher energy efficiency, reduced waste creation during construction and pollution, and increased health and satisfaction of the occupants. Though being beneficial to both the environment and the people, some challenges that face this method of construction are that upfront costs are typically higher than average due to the better quality of materials being used, complex techniques are used that are difficult to implement, and certifications are an added cost and may be complicated upon review of these standards [6].
However, for this study, performance comparisons for stick-frame construction and post-frame construction are only quantified through R-value calculations and thermal scanning. Due to time constraints and other external factors, the team was only able to come up with these two identifiers of a structure’s performance. For thermal scans, it is recommended for future researchers to conduct thermal scans on traditional stick-built homes. This should be done to have a visual comparison of the heat loss that both techniques are going through. However, as previously discussed, to identify a structure’s heat loss or heat gain, R-value calculations go hand in hand with thermal scans to accurately depict the efficiency of a structure. So, for R-value calculations, these were done with just Framing systems with R-20 batt insulation for both techniques. Moreover, for post-frame techniques, the team calculated 5’ and 6’ on center posts with their corresponding counterpart of 24” studs and 16” on center studs for a stick-built frame house. The values for Figure 11 define that there is a 31.22% difference between 6’ posts and 24” o/c studs and a 34.28% difference between 5’ posts and 16” o/c studs. These values prove that post-frame construction has higher R-values than the traditional stick-built structure, thus, post-frame structures constitute a higher-performance building. Although this does not mean that this structure is considered high-performance since there are still set standards that need to be taken into consideration before categorizing this specific structure as high-performing, it can be concluded that post-frames are better in terms of the R-values than the traditional stick-frame building.
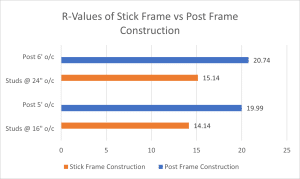
6.0 CONCLUSION
This study was initially based on Integrity Builders’ building techniques as they introduced new methods for construction. This prompted the team to gather information on building codes, traditional techniques, and costs. These were conducted to determine the current conditions of construction and to identify differences from post-frame construction that were introduced by Integrity Builders against the traditional stick-built method.
The team gathered thermal performance of the post-frame construction where data was acquired from R-value calculations and thermal cameras from drones flown around the site. To capture and analyze this data, the team used FLIR Tools and was able to find temperature scales on various components of the building. It was observed that with the materials and type of insulation installed within the structure, minimal heat loss was gathered. However, there were findings that some areas of the roof were not reached by the spray foam insulation that was applied but this was just a small area compared to the 30% heat loss that traditional stick-built homes experience. R-values were also considered in determining the thermal efficiency of homes. These values resulted in post-frame structures having a maximum value difference of 35% over the traditional method. This percentage difference is significant when determining efficiency in the structure, having this difference removed will make a positive impact on the efficiency of the building. Thus, this not only gives better efficiency for the home but also saves long-term costs. Overall, the thermal performance of post-frame structures is seen to be viable and better than traditional stick-built structures.
In terms of costs, these were analyzed after determining which technique is more efficient when it comes to thermal performance. The cost assessment for these two methods signified that the post-frame structures are significantly lower than the stick-built structure. This shows the economic ability of post-frame structures, and these cost savings can be used to further enhance the structure’s efficiency and performance like installing triple pane windows instead of the regular ones. Also, with these savings as well as an increase in performance, homeowners and builders can achieve economical and energy-responsible post-frame homes in comparison to traditional methods.
Based on the results of this study, having done all the research and calculations needed, the team was able to determine accurate differences between the two methods that were chosen for this study. The team recommends that post-frame construction having lower costs with higher efficiency than the traditional stick-built method equates to having a more economical and higher performing structure, thus, this can improve overall impact and can be considered applicable in terms of economic ability and efficiency.
6.0 RECOMMENDATIONS
For future researchers, the following recommendations provided by the team can be considered upon further study of the design given by this research:
- Implementation – The scope of the research is building techniques used in property limits based in Okotoks, Alberta and to be used in Calgary, Alberta. There are further geotechnical studies to be made in the soils of Calgary to ensure that the reviewed techniques in the study can be used.
- Incorporation of other disciplines – This study strictly looked at the costs and performance of the structural design of the proposed residential design. Including the costs and performance of electrical, mechanical, and architectural in comparison to the traditionally built residential buildings will give further analysis against the proposed design.
- High-performance standards – Due to time constraints in conducting this research, the team was not able to create a proposed design that met high-performance standards. A study can be conducted on the proposed design to meet these standards which allow for lower maintenance costs, increased occupant satisfaction, less construction waste, and higher energy efficiency. It could also include an energy model for better understanding.
- Other integrity-building techniques – Integrity Builders have other building products such as the storm bracket and their insulation package that this study did not implement in the design and analysis. These products could be implemented and tested for their performance and applicability in a design for residential housing.
7.0 ACKNOWLEDGEMENT
The team would like to dedicate this project study to the people who helped and guided the team in achieving and finishing our goals as fellow contributors to this institution as well as fellow contributors to the benefit of the community.
To the industry advisors, Integrity Builders, and Carleen Grant, who allowed the team to study and analyze their construction methods by providing everything the team needed from showing Integrity’s blueprints and cost estimates to inviting the team to Integrity’s wall factory. This allowed the team to accomplish the best version of our study.
To Matt Harding, a local mass residential stick builder who provided relevant cost information for the stick-built house. Allowed the team to draw an accurate conclusion of cost comparison between stick-built houses and post-frame houses.
To the team’s drone pilot Rick Duchscher, who helped take drone shots and thermal images on one of Integrity Builder’s projects. This allowed the team to perform and analyze one of the vital components of the study.
To Matthew Eidt, who served as the team’s building science expert and helped understand and impart his knowledge on how traditional buildings are made.
To the capstone adviser, Karen Riley, who served as the team’s guide and provided the team with suggestions and insights to produce the best outputs that the course demands. Also, with her guidance, the team was able to collaborate well complimenting each other’s strengths and weaknesses.
To the technical adviser, Ben Ellard, who served as the team’s primary mentor, giving bountiful knowledge that gave a very clear understanding of how the team can accomplish the objectives the research aims for.
To the professors, fellow course mates, and friends who gave knowledge and inspiration that resulted in the fruition of the research.
To the panelists, for helping the team clarify any points that the team may have discussed for the benefit of accomplishing the best version of the presentation.
To the institution, Southern Alberta Institute of Technology, offering the team the best education, forming future civil engineering technicians who uphold values, becoming advocates of progress and sustainability for the benefit of all.
And lastly, to each member of the team. Each one had a vital role in conducting this research, contributing all efforts to a maximum, resulting in the completion and acceptance of this study.
REFERENCES
[1] Perma Column Editors. “Advantages.” Perma Column. Accessed: Feb 13, 2024. [Online]. Available: https://permacolumn.com/builders/advantages.html.
[2] Perma Column Editors. “Perma-Column system.” Perma Column. Accessed: Feb 13, 2024. [Online]. Available: https://permacolumn.com/products/perma-column-system.html.
[3] IPS Foundation Insulation 2×6 2×8, Integrity Builders, Okotoks, AB, Calgary, for review, 2019. pp. 1. Accessed: Feb 13, 2024. [Text].
[4] Joe Di Noto. What Makes a High-Performance Building? 3 Fundamental Aspects 2023. Accessed: Feb 16, 2024. [Online] Available: https://learn.kaiterra.com/en/resources/high-performance-building-fundamental-aspects.
[5] Department of Energy. Thermographic Inspections. Accessed: Feb 16, 2024. [Online] Available: https://www.energy.gov/energysaver/thermographic-inspections.
[6] Second Nature. High-performance Building Standards. Accessed: Mar 15, 2024. [Online] Available: https://secondnature.org/solutions-center/high-performance-building-standards/.
[7] Patrick Lejtenyi. Thermal Imaging of Housing Stock can tell us where Energy Costs Will hurt. Concordia University. Accessed: April 03, 2024 [Online]. Available: https://www.concordia.ca/news/stories/2019/10/01/thermal-imaging-of-housing-stock-can-tell-us-where-energy-costs-will-hurt-say-concordia-researchers.html
[8] Mohammad Al-Homoud. Dictionary of Energy. Elsevier, 2015. Doi: https://doi.org/10.1016/c2009-0-64490-1.
[9] The Constructor. Frost Heave – How it works, effects, and prevention. Accessed: April 08, 2024. [Online] Available: https://theconstructor.org/practical-guide/frost-heave-effects-prevention/29754/
[10] Government of Canada. Canadian Climate Normals 1981-2010 Station Data: Temperature and Precipitation Graph for 1981 to 2010 Canadian Climate Normals CALGARY INT’L A, 2024. Accessed: April 08, 2024. [Online] Available: https://climate.weather.gc.ca/climate_normals/results_1981_2010_e.html?stnID=2205&autofwd=1
[11] NAHB Research Center. Revised Builder’s Guide to Frost Protected Shallow Foundations, 2004. Accessed: April 08, 2024. [Online] Available: https://www.homeinnovation.com/~/media/Files/Reports/Revised-Builders-Guide-to-Frost-Protected-Shallow-Foundations.pdf
GLOSSARY
Building techniques: Method or procedure by which a specific component of a structure is built.
Frost shields: Insulation system that protects concrete from frost heaves and prevents moisture from penetrating the soil surrounding the slab.
High performance: Standards that are set by certified industry organizations for building construction that focus on minimizing environmental impact and increasing overall efficiency.
Integrity: A construction firm based in Okotoks, Alberta served as the team’s industry partner and provided knowledge for the theories behind some of the new building techniques introduced in this study.
Perma-columns: Precast concrete columns that go underneath the subsurface and then support solid glulam wood columns for post-frame construction.
Post-Frame: Highly engineered building method that utilizes prefabricated columns and beams to form the wall system producing a structure with a variety of options for the interior and exterior systems.
Stick-Built: Traditional building method that uses stud walls and a foundation system that is built entirely on-site.
APPENDIX A: Ridged Insulation Assembly
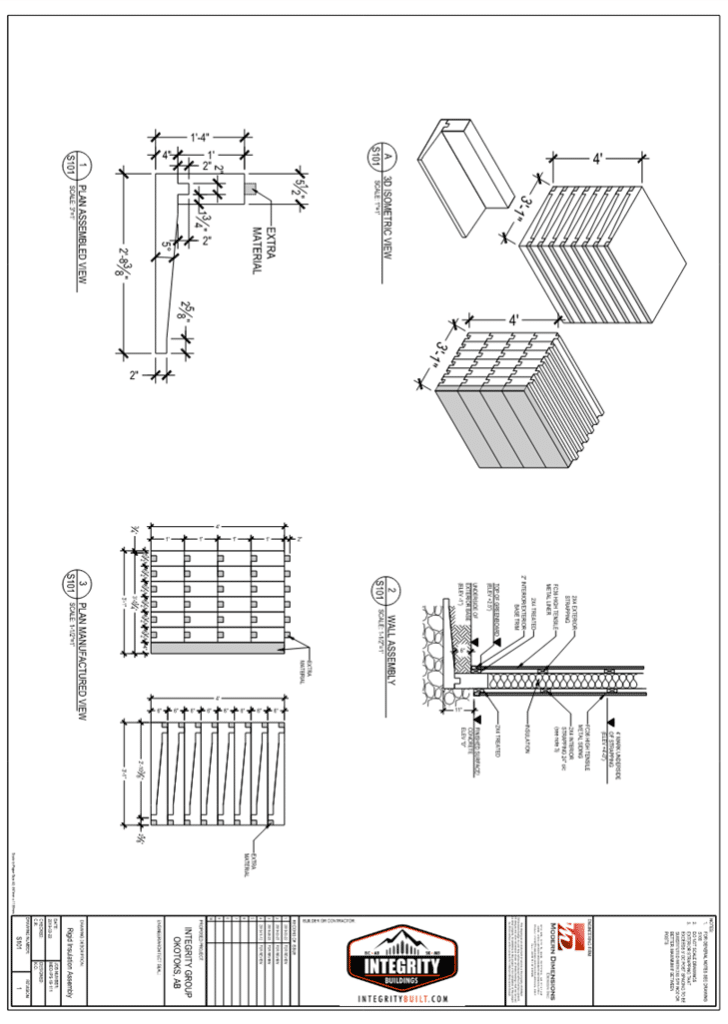
APPENDIX B: Example of Thermal Analysis Using FLIR Tools
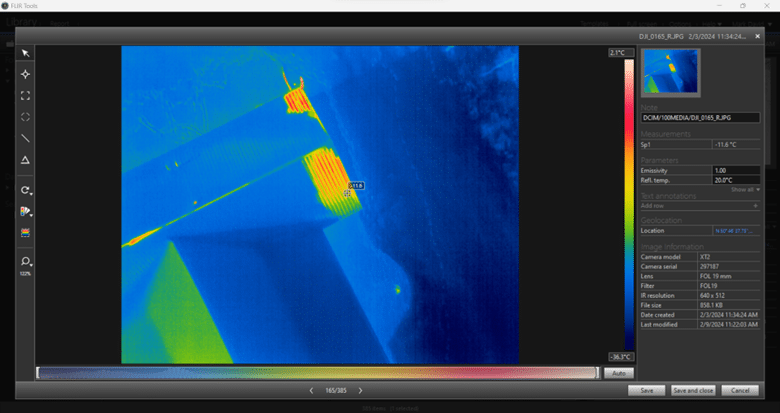
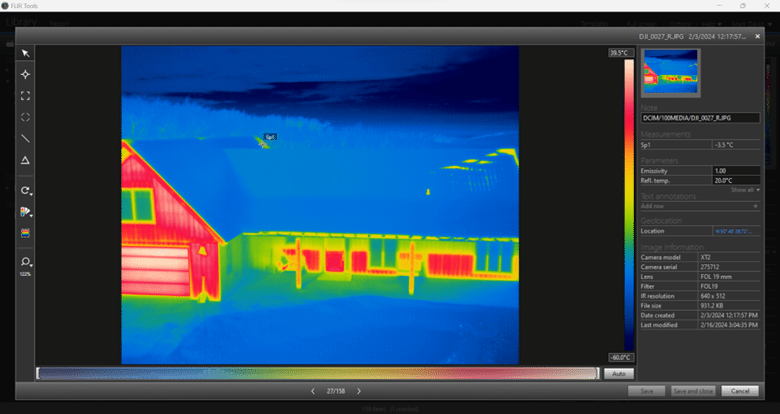
APPENDIX C: R-Value Calculations
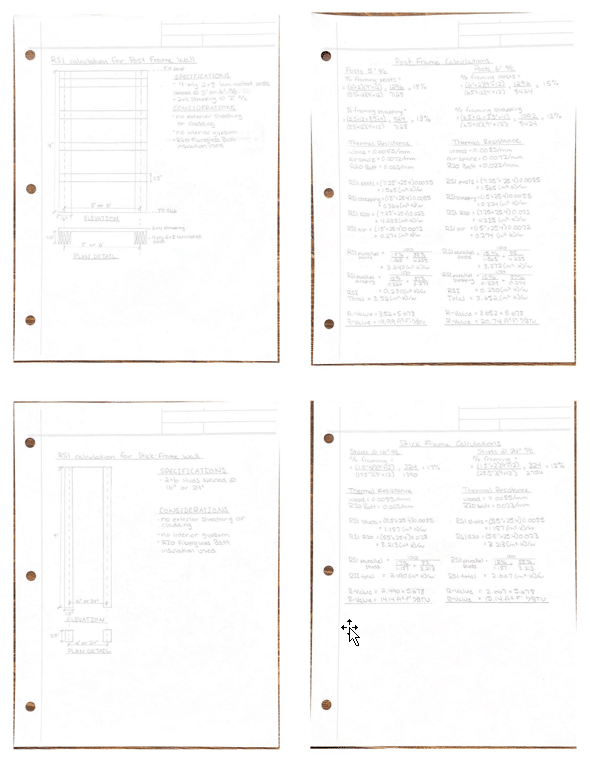
APPENDIX D: Cost Estimate for a Traditional Stick-Built House
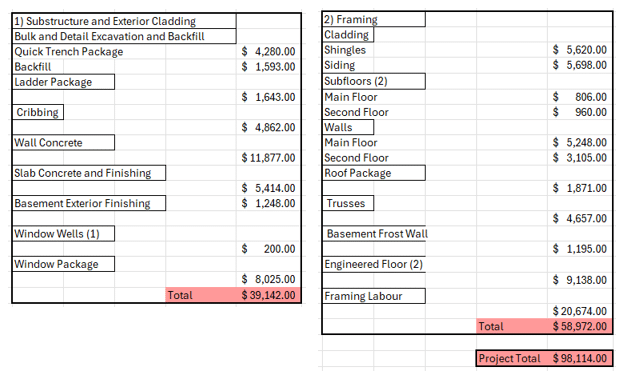
APPENDIX E: Cost Estimate for Integrity’s Post-Frame Construction
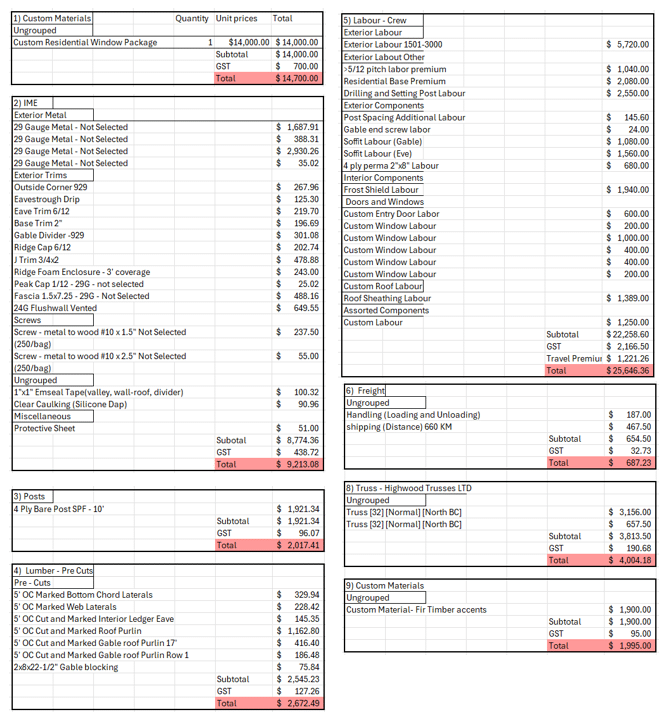
APPENDIX F: Continuation of Cost Estimate for Integrity’s Post-Frame Construction
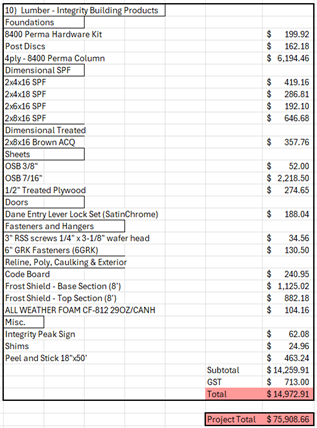
APPENDIX G: Gantt Chart
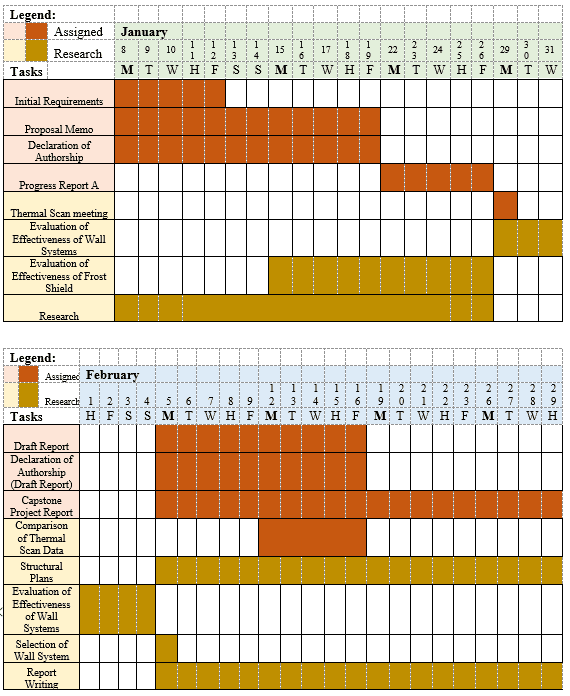
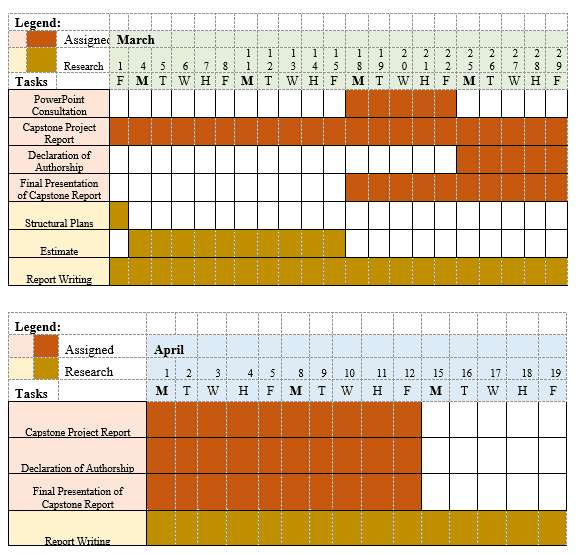